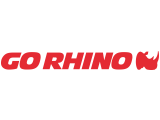
GO RHINO
Since 1975, Go Rhino has remained a leader in the development, design and manufacturing of innovative, stylish and extremely useful aftermarket automotive accessories. For over 30 years, Go Rhino has taken pride in offering products that allow the trucks and SUV owner to enjoy the most from their vehicle.
Our family-owned and operated company has a long, rich history developing, engineering, and manufacturing some of the most innovative products for your vehicle. Since originating the first modular grille guard over 30 years ago, Go Rhino has established a reputation for being FIRST in introducing superior quality, new and original products to the market and quickly setting the industry standard.
In 2004, Go Rhino was pleased to partner with XTREME RACKS, as two companies with one vision! Together we are determined to narrow the gap between functionality, rugged good looks, and durability with all of our award-winning truck and SUV products.
Many of our competitors use plastic parts on their sidesteps while we only use non-slip Super Grip rubber step pads. Go Rhino also offers the patented grille guard with built-in step and shippable wheel-to-wheel sidebars. Our products are also produced with the highest of standards. We monitor, document, and inspect every part and every process, and as a result, have earned the prestigious ISO9001 certification that is your assurance of consistent quality and commitment to excellence. The ISO (International Organization for Standardization) is the world's largest developer of international standards. These standards give state of-the-art specifications for products and services. The ISO was created to provide assurance to consumers that being provided great products and services while also making industry more effective and efficient.
Our manufacturing facility is staffed with talented, skilled, and passionate personnel who build each Go Rhino product to the highest standards while utilizing the latest technology and processes. Hundreds of hours go into the development, testing, and fitting of each product before it is approved for manufacturing.
The research and development team work tirelessly to bring each new product to life. Once a product is approved, our manufacturing team goes to work. Skilled, trained technicians man some of the most advanced machines for cutting, bending, and preparing our parts for assembly. Precision jigs ensure that each piece fits to exacting standards with welds created by experienced craftsmen or the best robotic welders. Our processes include constant inspections for the best fit. Once assembly is complete, you can count on the highest quality and best-looking finishes, whether it be our black powder coat, textured black powder coat, chrome, or mirrored polished stainless steel finishes. All of our finishes meet or exceed the OE standards for quality and durability. The most advanced, automated powder coat line is constantly monitored for uniform gloss and thickness.
Once the parts are complete, they are packed carefully and stocked in one of our two giant warehouses serving each coast. As product is received, it is placed in one of four staging areas based on how popular the product is and how often it is ordered. Our quickest-moving products are stocked at maximum capacity to ensure that they are in stock for immediate same-day shipping, if needed.
questions? contact us.